The use of fused silica quartz ceramic rollers from Kamroller Special Ceramics Co., Ltd. marks a transformative step in the glass manufacturing process. As real-world success stories attest, these advanced rollers not only enhance efficiency but also contribute to cost-effectiveness and long-term sustainability. With considerations for glass manufacturers, maintenance best practices, and insights into future trends, it is clear that the fusion of advanced ceramic technology and glass manufacturing is paving the way for a brighter and more innovative future.
I. Introduction
In the intricate world of glass manufacturing, the role of rollers is pivotal in ensuring the smooth and efficient production of high-quality glass products. These cylindrical components play a crucial part in shaping and conveying molten glass, making them indispensable in the glass factory setting. One key Fused Silica Quartz Ceramic Roller For Glass Factory in this domain is Kamroller Special Ceramics Co., Ltd., offering state-of-the-art fused silica quartz ceramic rollers as a cornerstone in the glass production process.
II. What is Fused Silica Quartz Ceramic?
A. Definition and Characteristics
Fused silica quartz ceramic is a specialized material known for its remarkable combination of properties that make it an ideal choice for various industrial applications. Composed primarily of silicon dioxide, fused silica quartz ceramic exhibits excellent thermal stability, high-temperature resistance, and exceptional chemical inertness. These qualities make it stand out in demanding environments like glass manufacturing.
B. Key Properties for Glass Manufacturing
The unique properties of fused silica quartz ceramic make it particularly well-suited for roles in glass factories. Its high-temperature resistance ensures the rollers can withstand the intense heat of molten glass, while low thermal expansion guarantees consistent performance even under extreme conditions. Additionally, the material’s chemical inertness and purity contribute to the overall quality of the glass produced.
C. Comparison with Other Materials
When considering materials for rollers in glass factories, fused silica quartz ceramic outshines its competitors. Compared to traditional materials like steel or other ceramics, fused silica quartz ceramic offers superior thermal stability and resistance, providing a longer lifespan and increased efficiency in the glass production process.
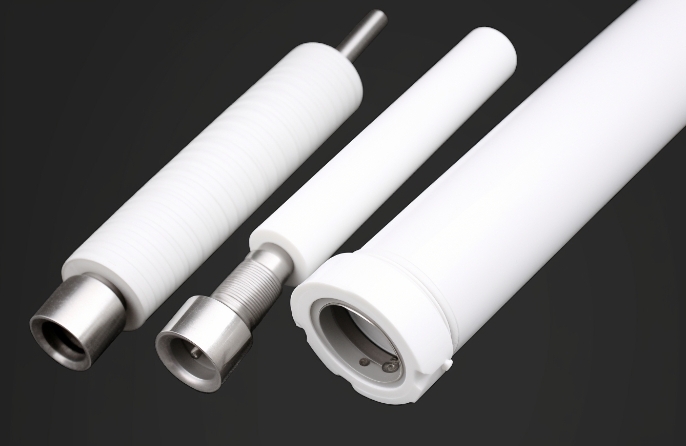
III. Role of Rollers in Glass Production
A. Glass Production Process
Understanding the importance of rollers begins with grasping the intricacies of the glass production process. In a typical glass factory, raw materials such as silica, soda ash, and limestone are melted at high temperatures to form molten glass. This molten glass is then shaped, cooled, and cut into the final product. Throughout this process, rollers play a pivotal role in conveying and shaping the molten glass.
B. Importance of Rollers
Rollers serve as the backbone of glass production, facilitating the smooth movement of the molten glass through various stages. They aid in shaping the glass into the desired form and ensuring consistent thickness. The proper functioning of rollers directly impacts the quality and efficiency of the glass manufacturing process.
C. Fused Silica Quartz Ceramic Rollers’ Enhancement
Fused silica quartz ceramic rollers from Kamroller Special Ceramics Co., Ltd. elevate the glass manufacturing process to new heights. The exceptional properties of this specialized ceramic ensure that the rollers perform optimally under the demanding conditions of high-temperature environments. The precision and reliability of fused silica quartz ceramic rollers contribute to a more efficient and streamlined glass production process.
IV. Advantages of Fused Silica Quartz Ceramic Rollers
A. High Temperature Resistance and Thermal Stability
Fused silica quartz ceramic rollers can withstand extreme temperatures, making them invaluable in glass factories where the heat generated during the glassmaking process is intense. This high-temperature resistance ensures consistent performance and longevity.
B. Low Thermal Expansion for Consistent Performance
The low thermal expansion of fused silica quartz ceramic means that the rollers maintain their shape and functionality even when exposed to rapid temperature changes. This consistency is essential for producing high-quality glass with uniform thickness.
C. Wear Resistance and Durability
In the harsh conditions of glass production, wear and tear are inevitable. Fused silica quartz ceramic rollers exhibit exceptional wear resistance, ensuring a longer lifespan and reduced maintenance requirements. This durability translates to cost savings for glass manufacturers.
D. Chemical Inertness and Purity
The chemical inertness and purity of fused silica quartz ceramic contribute to the overall quality of the glass produced. The rollers do not introduce impurities into the molten glass, resulting in a purer final product with enhanced optical and mechanical properties.
E. Reduced Maintenance and Downtime Benefits
The longevity and resilience of fused silica quartz ceramic rollers translate into reduced maintenance needs and downtime for glass factories. This not only improves operational efficiency but also minimizes production interruptions, ultimately benefiting the bottom line.
V. Applications in Glass Factories
A. Overview of Specific Applications
Fused silica quartz ceramic rollers find a multitude of applications within the intricate landscape of glass manufacturing. From the initial stages of conveying molten glass to the final shaping and cooling processes, these rollers play a crucial role in ensuring the efficiency and precision of the entire production line. Their specific applications include conveying molten glass, shaping the glass into desired forms, and maintaining uniform thickness throughout the manufacturing process.
B. Efficiency Improvement in Different Stages
Examples abound of how fused silica quartz ceramic rollers from Kamroller Special Ceramics Co., Ltd. enhance efficiency at various stages of glass production. In the molten glass conveying stage, these rollers’ high-temperature resistance ensures seamless movement, preventing disruptions that can hinder production flow. During shaping, the low thermal expansion and wear resistance contribute to consistent performance, resulting in precisely formed glass products. These rollers prove invaluable in maintaining uniform thickness, a critical factor in producing high-quality glass.
VI. Case Studies or Success Stories
A. Real-world Examples
Glass factories worldwide have experienced transformative outcomes after implementing fused silica quartz ceramic rollers. One notable case is the Glass Manufacturing Plant, which witnessed a significant reduction in maintenance downtime and increased production efficiency. The implementation of Kamroller’s ceramic rollers not only improved the quality of their glass products but also showcased a positive impact on the bottom line.
B. Positive Outcomes and Cost-effectiveness
In the aforementioned case study, the introduction of fused silica quartz ceramic rollers led to increased productivity due to reduced maintenance requirements and improved durability. The cost-effectiveness of these rollers became evident as the plant experienced fewer replacements and repairs, translating into substantial long-term savings. This success story underscores the tangible benefits that Kamroller’s advanced ceramic technology brings to glass manufacturing.
VII. Considerations for Glass Manufacturers
A. Factors to Consider
When glass manufacturers are in the process of choosing rollers for their factory, several factors come into play. Temperature resistance, wear resistance, and thermal stability are paramount considerations. Fused silica quartz ceramic rollers excel in all these aspects, offering manufacturers a reliable solution for the demanding conditions of glass production. Additionally, compatibility with specific glass compositions, ease of installation, and overall lifecycle costs should be taken into account when making this crucial decision.
B. Maintenance Tips and Best Practices
Maintaining the optimal performance of fused silica quartz ceramic rollers requires periodic inspection and cleaning. Regular checks for wear and tear, as well as the application of recommended lubricants, ensure longevity. Best practices also involve following Fused Silica Quartz Ceramic Roller For Glass Factory guidelines for installation and handling. Kamroller Special Ceramics Co., Ltd. provides comprehensive maintenance guidelines to maximize the lifespan and efficiency of their ceramic rollers.
C. Potential Challenges and Solutions
While fused silica quartz ceramic rollers offer numerous advantages, challenges may arise, such as potential breakages due to mishandling or extreme conditions. To overcome these challenges, proper training for handling and installation is crucial. Additionally, close collaboration with the manufacturer can address specific concerns and provide tailored solutions. Kamroller Special Ceramics Co., Ltd. offers technical support and assistance to help glass manufacturers navigate potential challenges effectively.
Conclusion
In conclusion, the role of fused silica quartz ceramic rollers from Kamroller Special Ceramics Co., Ltd. in the glass manufacturing process cannot be overstated. These advanced components not only withstand the demanding conditions of high-temperature glass production but also contribute significantly to the efficiency, consistency, and quality of the final glass products. As the glass industry continues to evolve, the reliance on innovative materials like fused silica quartz ceramic is set to grow, ensuring a brighter and more transparent future for glass manufacturing.
Post time: 1 月-10-2024