Fused silica rollers are essential components in various industrial applications, providing exceptional heat resistance, high strength, and excellent surface quality. These rollers find extensive use in glass manufacturing, solar panel production, semiconductor processing, and other precision industries.
In this article, we will explore the different types of fused silica rollers available, and their classifications, and highlight Kamroller as a leading manufacturer of high-quality fused silica rollers.
What Is A Fused Silica Roller?
Fused silica rollers are specialized components used in various industries for their exceptional thermal properties and mechanical strength.
These rollers are made from fused silica, a high-purity form of silicon dioxide, and find extensive applications in glass manufacturing, semiconductor processing, solar panel production, and other precision industries.
Composition and Manufacturing Process
Fused silica rollers are primarily composed of silicon dioxide (SiO2) in their amorphous or glassy form. The manufacturing process involves melting high-purity silica at very high temperatures and then rapidly cooling it to form a solid material with excellent thermal stability and mechanical properties.
Mechanical Strength and Durability
Fused silica rollers exhibit high mechanical strength, making them capable of withstanding heavy loads and maintaining their shape under pressure.
They possess excellent hardness and wear resistance, ensuring prolonged service life even in demanding industrial environments. These properties make fused silica rollers suitable for applications where precise and consistent material processing is crucial.
Classification of Fused Silica Rollers:
Fused silica rollers can be classified based on different criteria, including their composition, surface finish, and applications. Let’s delve into each classification method:
1) Composition-Based Classification:
Fused silica rollers can be categorized based on the type of fused silica used in their manufacturing process. The two primary types are:
l 99.9% Fused Silica Rollers:
These rollers are made from high-purity fused silica, ensuring excellent thermal stability and resistance to thermal shock. They are ideal for applications that require prolonged exposure to high temperatures, such as glass tempering and annealing processes.
l Doped Fused Silica Rollers:
Doping fused silica with specific materials can enhance its properties. For example, zirconium dioxide (ZrO2) doping increases the mechanical strength and wear resistance of the rollers, making them suitable for demanding applications like solar panel production and semiconductor wafer processing.
2) Surface Finish-Based Classification:
The surface finish of fused silica rollers plays a crucial role in their performance. Different surface finishes are suitable for specific applications. Here are two common types:
l Polished Fused Silica Rollers:
These rollers undergo a meticulous polishing process to achieve an ultra-smooth surface finish. They are widely used in applications that require precise and uniform pressure distribution, such as LCD glass manufacturing and optical fiber drawing.
l Textured Fused Silica Rollers:
Textured rollers feature a patterned surface that improves grip and prevents slippage during the processing of materials. They are commonly used in applications like silicon wafer manufacturing, where controlled material movement is essential.
Kamroller: Your Source For High-Quality Fused Silica Rollers
When it comes to sourcing top-notch fused silica rollers, Kamroller is a name you can trust. As a professional and advanced manufacturer, Kamroller offers a wide range of fused silica rollers that cater to diverse industrial needs. Here’s why Kamroller stands out:
Superior Quality:
Kamroller’s fused silica rollers are manufactured using high-purity materials and advanced production techniques, ensuring exceptional quality and performance. They are designed to withstand extreme temperatures, heavy loads, and corrosive environments.
Customization Options:
Kamroller understands that different industries have unique requirements. Therefore, they offer customization options to tailor the fused silica rollers according to specific dimensions, surface finishes, and composition variations to meet customers’ exact needs.
Extensive Industry Experience:
With years of experience in the field, Kamroller has gained extensive knowledge and expertise in fused silica roller manufacturing. Their team of professionals ensures strict quality control at every stage of production, resulting in reliable and durable rollers.
Competitive Pricing:
Kamroller strives to offer competitive pricing without compromising on quality. They understand the importance of cost-effectiveness in industrial operations and aim to provide value for money.
Exceptional Customer Support:
Kamroller is committed to providing excellent customer service. Their knowledgeable and responsive support team assists customers in choosing the right fused silica rollers and provides prompt solutions to any queries or concerns.
An Example Of High-Quality Fused Silica Rollers From Kamroller:
When it comes to high-quality fused silica rollers, Kamroller is a trusted manufacturer known for its advanced products. One such example is the Fused Silica Ceramic Roller, which offers exceptional performance and versatility in various industries.
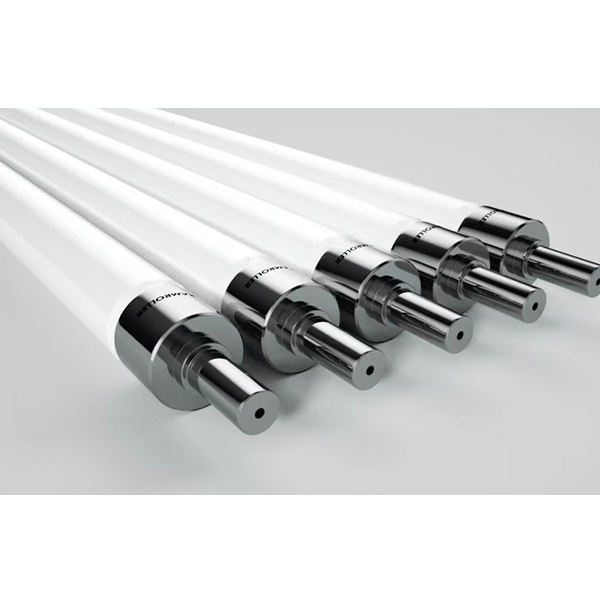
In this section, we will explore some key product information about Kamroller’s Fused Silica Ceramic Roller, showcasing its benefits and applications.
1. Smooth and Non-Porous Surface
The Fused Silica Ceramic Roller features a smooth and non-porous surface, minimizing material adhesion and sticking. This characteristic is particularly advantageous in applications that require precise material handling and uniformity. By facilitating smooth and consistent material transfer, the roller ensures efficient and reliable processing.
2. Precise Dimensions and High-Dimensional Stability
The Fused Silica Ceramic Roller is designed with precise dimensions and offers high dimensional stability. These features enable accurate and reliable material transport, ensuring consistent product quality. With the roller’s precise dimensions, you can achieve the desired results in your manufacturing or processing operations.
3. Excellent Wear Resistance
The Fused Silica Ceramic Roller exhibits excellent wear resistance, minimizing surface deterioration over time. This property ensures consistent and reliable performance throughout its extended service life. By reducing the need for frequent roller replacements, downtime is minimized, and maintenance costs are reduced, optimizing overall productivity and efficiency.
Final words:
Fused silica rollers are essential components in various industries, offering exceptional thermal stability, strength, and surface quality.
By understanding the different types of fused silica rollers available, their classifications, and the advantages of choosing a reliable manufacturer like Kamroller, you can make informed decisions for your specific application requirements.
Whether you need polished rollers for precise glass manufacturing or textured rollers for controlled material movement, Kamroller offers a comprehensive range of high-quality fused silica rollers to meet your needs. Invest in top-notch fused silica rollers for improved productivity, efficiency, and long-term reliability in your industrial processes.
Post time: 6 月-16-2023